Jlg 20vp Service Manual
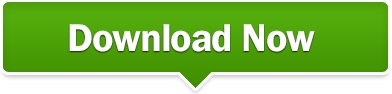
Read online or download PDF • Page 60 / 96 • JLG 20VP (3120849) Service Manual User Manual • JLG Special machinery. Results 97 - 144 of 378 - JLG 120HX Boom LIft Repair Shop Service Maintenance Manual owner operator. JLG 10VP 15VP 20VP Operator and Safety manual.
. Service and Maintenance Manual Model 10VP 15VP 20VP 3120728 June 14 2001 ANSI. FOREWORD The purpose of this manual is to provide users with the operating procedures essential for the promotion of proper machine operation for its intended purpose. It is important to over-stress proper machine usage.
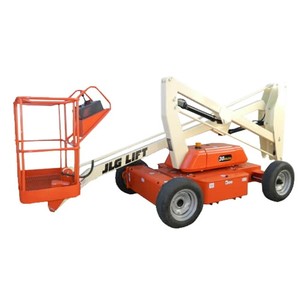
All information in this manual should be READ and UNDERSTOOD before any attempt is made to operate the machine. YOUR OPERATING MANUAL IS YOUR MOST IMPORTANT TOOL - Keep it with the machine. REMEMBER ANY EQUIPMENT IS ONLY AS SAFE AS THE OPERATOR. This page left intentionally blank. INTRODUCTION - MAINTENANCE SAFETY PRECAUTIONS INTRODUCTION - MAINTENANCE SAFETY PRECAUTIONS A. MAINTENANCE This section contains the general safety precautions which must be observed during maintenance of the aerial platform.
It is of utmost importance that maintenance personnel pay strict attention to these warnings and precautions to avoid possible injury to themselves or others or damage to the equipment. INTRODUCTION - MAINTENANCE SAFETY PRECAUTIONS This page intentionally left blank b – JLG Lift – 3120728. EFFECTIVITY PAGE EFFECTIVITY CHANGES September 15, 1997 – Original Issue of Manual January 10, 1998 – Change 1– Pages Affected: Revision Log - Page c Table of Contents - Page ii Section 3 - Pages 3-8 & 3-9 February 7, 2000 – Revised – Pages Affected: Section-1, Page 1-5, Table 1-5. Section-2, Page 2-18, Table 2-3.
(removed lube check requirement for drive wheel gear box) March 22, 2000– Revised – Added 20VP UL-EE Option. EFFECTIVITY PAGE This page intentionally left blank d – JLG Lift – 3120728. TABLE OF CONTENTS SUBJECT - SECTION, PARAGRAPH PAGE NO.
SECTION INTRODUCTION -MAINTENANCE SAFETY PRECAUTIONS A B C General.a Hydraulic System Safety.a Maintenance. TABLE OF CONTENTS LIST OF FIGURES FIGURE NO. TITLE PAGE NO.
Hydraulic Pressure Setting - Adjustment Screw Located at Base of Pump Motor.1-3 Hydraulic Pressure Gauge Installation.1-3 Torque Chart. TABLE OF CONTENTS 3-9 3-10 3-11 3-12 3-13 3-14 3-15 3-16 3-17 3-18 3-19 3-20 3-21 3-22 3-23 3-24 3-25 3-26 3-27 3-28 3-29 3-30 3-31 3-32 3- Drive Motor/Circuit Check.3-21 Brake Switch/Circuit Check.3-21 Won’t Drive with Platform Elevated. TABLE OF CONTENTS This page intentionally left blank iv – JLG Lift – 3120728.
SECTION 1 - SPECIFICATIONS SECTION 1. SPECIFICATIONS 1.1 Batteries/Battery Charger CAPACITIES Batteries (2) – 12 Volt / 80 Amp Hour – System Voltage Deep CycleMarine - RV All VP Models –24 Volt DC (2 - 12 volt DC batteries) Battery Charger – U.S.A./CAN. –120 Volt A.C.

/ 60 Hz input Hydraulic Oil Reservoir Brazil - 220 Volt A.C./ 60 Hz input All VP Models – 5 qts. (4.7 ltr.) 24 volt, 10 amp output with 2 amp finish 1. SECTION 1 - SPECIFICATIONS Base Footprint 1.5 VP Series - 32 in. (81cm) width 56 in. (1.42m) length LUBRICATION Hydraulic Oil Max. Platform Height (mast extended) Hydraulic oils must have anti-wear qualities at least to API Service Classification GL-3, and sufficient chemical stability for mobile hydraulic system service.
JLG Industries, recommends Mobilfluid 424 hydraulic oil, which has an SAE viscosity of 10W-30 and a viscosity index of 152. 10VP – 10 ft. 6 in.(3.2m) 15VP – 15 ft.(4.
SECTION 1 - SPECIFICATIONS 1.6 HYDRAULIC PRESSURE ADJUSTMENT Adjust system pressure so that platform will raise with rated capacity in platform. The following are recommended factory pressure settings; VP10,VP15 –1000 psi VP20 – 2500 psi Turning adjustment screw clockwise increases system pressure, turning screw counterclockwise decreases system pressure. SECTION 1 - SPECIFICATIONS Figure 1-3. Torque Chart. SECTION 1 - SPECIFICATIONS 6 1 2 3 4, 5 Figure 1-4. Lubrication Chart. Table 1-6.Lubrication Intervals for Various Components INTERVAL HOURS ITEM COMPONTENT NO/TYPE LUBE POINTS LUBE/METHOD 3 6 MONTHS MONTHS 150 Hrs.
1 Hydraulic Oil Fill To Line on Reservoir 5 Qt. SECTION 1 - SPECIFICATIONS This page intentionally left blank 1-6 – JLG Lift – 3120728. SECTION 2 - SERVICE PROCEDURES SECTION 2. SERVICE PROCEDURES 2.1 GENERAL This section provides general information to assist in the performance of maintenance on the personnel lift. Descriptions, techniques and specific procedures are designed to provide the safest and most efficient maintenance for use by personnel responsible for ensuring the correct installation and operation of machine components and systems. SECTION 2 - SERVICE PROCEDURES apply pressure to the outer race.
If the bearing is to be installed on a shaft, apply pressure to the inner race. Gaskets Check that holes in gaskets align with openings in the mating parts. If it becomes necessary to hand-fabricate a gasket, use gasket material or stock of equivalent material and thickness. Be sure to cut holes in the right location, as blank gaskets can cause serious system damage. Bolt Usage and Torque Application Use bolts of proper length.
SECTION 2 - SERVICE PROCEDURES Tight Joints: All joints in the leaf chain should flex freely. On leaf chain, tight joints are usually caused by rust/corrosion, or the inside plates “walking” off the bushing. Limber up rusty/corroded chains (after inspecting care fully) with a heavy application of oil (preferably a hot oil dip). Tap inside “walking” plates inward; if “walking” persists, replace the chain. SECTION 2 - SERVICE PROCEDURES can cause wear or damage to the components and generally results in faulty operation.
Every precaution must be taken to keep hydraulic oil clean, including reserve oil in storage. 2.4 POSITIONING LIFT FOR ACCESS TO COMPONENTS LOCATED UNDER THE BASE FRAME Cloudy oils indicate a high moisture content which permits organic growth, resulting in oxidation or corrosion.
If this condition occurs, the system must be drained, flushed, and refilled with clean oil. SECTION 2 - SERVICE PROCEDURES 2.5 DRIVE MOTOR COMPONENT SERVICE PROCEDURES Torque Limiting Clutch Maintenance Checking Clutch - Torque Setting (ft. Lb.) NOTE: Check that the machines brakes are engaged before applying torque to the rear drive wheels. Remove the drive wheels from the drive axles. VP Series machines are equipped with a torque limiting clutch coupling on each drive axle. The clutch is mounted inline on the drive axle between the drive wheel and the drive motor gear box. SECTION 2 - SERVICE PROCEDURES Torque Limiting Clutch Adjustment Drive Motor Brake Adjustment/Removal NOTE: The large adjusting nut on the side of the clutch assembly is a standard type thread.
If the torque (slip) setting of the clutch assembly is under spec (by more than 35 ft. Lb.), the large adjusting nut must be (tightened) turned clockwise to increase the torque setting.
If the torque (slip) setting is over spec (over 185 ft. SECTION 2 - SERVICE PROCEDURES FRICTION BRAKE DISK FRICTION BRAKE DISK MOUNTING PLATE ARMATURE PLATE MAGNETIC COIL (Not Energized) MANUAL RELEASE ARM/ ADJUSTMENT SCREW MOUNTING PLATE ARMATURE PLATE 0.006” GAP BETWEEN ARMATURE PLATE AND MAGNETIC COIL MAGNETIC COIL (Energized) MANUAL RELEASE ARM/ ADJUSTMENT SCREW 0.020” GAP UNDER SCREW HEAD BETWEEN ARMATURE PLATE 0.006” GAP BETWEEN FRICTION DISK AND ARMATURE PLATE 0. SECTION 2 - SERVICE PROCEDURES Brake Assembly Removal 6. Reconnect the manual release brake cable to the manual release lever (Y shaped lever) and adjust cable so brakes are released when manual release lever is in the down position. (See Figure 2-6.) 1. Lift the machine to gain access to the underside (See Section 2-4., 'Positioning Lift For Access To Components Located Under The Base Frame').
SECTION 2 - SERVICE PROCEDURES Drive Motor Removal 5. Disconnect the wiring connectors to the drive motor and the brake assembly on either or both sides, depending on which drive assembly(ies) is being removed. (See Figure 2-7.) The VP drive motors consist of three sections, the gear box atttached to the rear of the drive motor, the electric drive motor itself, and the brake assembly mounded at the front of the drive motor. SECTION 2 - SERVICE PROCEDURES Gear Box Disassembly/Assembly IF REMOVING THE COMPLETE DRIVE ASSEMBLY, IT WEIGHS APPROXIMATELY XX LB.
AND WILL REQUIRE ASSISTANCE TO LOWER. PREFERABLY USE A MOVABLE TRANSMISSSION OR OTHER HYDRAULIC JACK TO CAREFULLY LOWER ASSEMBLY FROM UNDER MACHINE. Carefully remove the four (4) nuts and washers (outer most holes on the drive assembly weldment) from the carriage bolts attaching the drive motor assembly to the base frame. SECTION 2 - SERVICE PROCEDURES NOTE: The gear oil can be drained out when the side cover is removed in the next step. Remove the side cover from the gear box with the drive shaft side pointing down, then tilt drive motor/gear box assembly to drain the oil into a suitable container. Remove the four (4) hex cap screws securing the side cover to the gear box housing, and remove the side cover and rubber seal ring.
SECTION 2 - SERVICE PROCEDURES Final Gear Box Assembly that gear set align the drive shaft bearing and wiggle it into it’s seat. When both are seated continue to next step. If necessary, install a new drive shaft lip seal into the drive shaft hole in the gear box housing before assembling the drive shaft gear set into the gear box. SECTION 2 - SERVICE PROCEDURES Brush Removal (See Figure 2-12.) Drive Motor Brush Replacement Each drive motor contains two (2) brushes, the brushes are located under the two (2) large round slotted brush caps on the front end of each drive motor.
BRUSH CAP Removal of the brushes also requires the removal of the drive motor(s) from the machine, see procedure described earlier in this section for instructions to remove the drive motors. SECTION 2 - SERVICE PROCEDURES Brush Reassembly (See Figure 2-12.) MAKE CERTAIN THAT THE GROUND WIRE IS SECURELY RECONNECTED TO THE GROUND TERMINAL IF REMOVED. LEADS, INTERNAL TO THE SHEILD, MUST BE ROUTED AWAY FROM THE ARMATURE, (E.G.: BE CLOSE TO THE INSIDE WALL OF THE ALUMINUM SHIELD) TO PREVENT A SAFETY HAZARD AND/OR DAMAGE TO THE MOTOR. Install the brush (pig-tail) terminal end under the screw on the brush box in the same manner as the old brush that was removed and tighten the screw. SECTION 2 - SERVICE PROCEDURES 2.6 3. Turn on power to the platform control, nine (9) LED’s will flash rapidly on the platform control touch pad. PLATFORM CONTROL BOX SERVICE PROCEDURES 4.
Depress the horn switch pad, the alarm will sound for about one (1) second, then release the horn pad. Joystick Calibration Procedure 5. Now release the joystick to the neutral position.
Turn off all power to the platform control. Turn off system power. SECTION 2 - SERVICE PROCEDURES Lower Half Of Housing Removal Platform Control Box Disassembly 1. Position the control box upside down and remove the six (6) screws attaching the lower half of the housing to the upper half of the control box housing. DO NOT ATTEMPT TO DISASSEMBLE THE PLATFORM CONTROL BOX IF MACHINE IS STILL UNDER WARRANTY. OPENING THE PLATFORM CONTROL BOX WHILE THE MACHINE IS UNDER WARRANTY WILL VOID THE WARRANTY.
IF UNDER WARRANTY REQUEST A REPLACEMENT BOX FROM THE FACTORY. SECTION 2 - SERVICE PROCEDURES 3. Remove the four (4) screws attaching the circuit board to the upper housing. Emergency Stop Switch Removal 1. Remove the switch part of the emergency stop switch by carefully prying upward at the corner of the switch using a straight blade screwdriver.
This will seperate the switch from the reset button part of the emergency stop button assembly. NOTE: If reusing the circuit board be careful when unsoldering component wires DO NOT OVERHEAT BOARD. SECTION 2 - SERVICE PROCEDURES 3. Remove the reset button part of the emergency stop switch by unscrewing the collar on the inside end of the reset button assembly. Touch Pad Switch Removal 1. Unplug the touch pad ribbon cable connector from the circuit board connector socket. (See Figure 215.) 2.
Using a thin tool, start by lifting an edge of the touch pad switch and slowly peel away it from the face of the upper housing until completely free. Speed Control Switch Removal 1. SECTION 2 - SERVICE PROCEDURES Speed Control Switch Installation 1.
Use the following illustrations to reattach the wires from the speed control switch to the circuit board. WIRES FROM JOYSTICK CONTROL (Later Model Joystick w/Drive Enable on Knob) WHITE (light gauge) YELLOW (light guage) CIRCUIT BOARD COMPONENT SIDE CIRCUIT BOARD COMPONENT SIDE ORANGE WHITE W/ORG GREEN 2. If damaged replace the gasket between upper housing surface and the joystick mounting surface before assembling. SECTION 2 - SERVICE PROCEDURES nector from the touch pad switch through the slot at the top of the housing. Before pressing the touch pad adhesive side to the upper housing mounting surface, visually align the touch pad edges with the edges of the recess in the housing mounting surface. SECTION 2 - SERVICE PROCEDURES Printed Circuit Board Replacement Battery Charger Part Replacement 1.
Disconnect the wide wiring connector from the end of the circuit board. Cover Removal 1. Remove the eight (8) screws on the sides of the charger cover and remove cover.
Remove the four (4) screw attaching the card to the front face of the charger chassis. Remove the circuit board. Shunt Assembly Replacement Transformer Replacement 1. SECTION 2 - SERVICE PROCEDURES AC Circuit Breaker Replacement Interlock Relay Replacement 1. Disconnect the wiring connected to the relay. Disconnect wiring connected to the breaker poles. Remove the two (2) nuts securing the interlock relay to the chassis base.
Remove the two (2) nuts securing the AC breaker to the chassis screws. Remove the relay. Remove the breaker from the chassis. SCR Rectifier Replacement (Either Side) 1.
Remove the wiring from the SCR Rectifier. SECTION 2 - SERVICE PROCEDURES 2.8 HYDRAULIC LIFT CYLINDER REMOVAL, INSPECTION AND REBUILD HYDRAULIC CYLINDERS ARE DESIGNED TO HOLD HYDRAULIC FLUID UNDER HIGH PRESSURE. BE SURE ALL APPROPRIATE MEASURES ARE TAKEN TO RELIEVE RESIDUAL PRESSURE IN THE CYLINDER BEFORE DISCONNECTING LINES. Lift Cylinder Removal Removal of the hydraulic lift cylinder without removing the mast from the machine requires laying the machine on it’s back (hood side) with the platform end on top. SECTION 2 - SERVICE PROCEDURES Lift Cylinder Component Inspection Cylinder Assembly Cylinder Rod (See Figure 2-17.) There should be no scratches or pits deep enough to catch the fingernail. Pits that go to the base metal are unacceptable.
Scratches that catch the fingernail but are not to the base metal, less than 0.5 inch long and primarily in the circumferential direction are acceptable provided they cannot cut the rod seal. SECTION 2 - SERVICE PROCEDURES RETAINING RING GROOVE WEAR RING PISTON SEAL O-RING O-RING CYLINDER HEAD RETAINING RING BACKUP RING ROD SEAL ROD WIPER CYLINDER TUBE ASSEMBLY LOCKNUT (Torque 175-200 Ft. Lb.) PISTON WHEN ASSEMBLING CYLINDER APPLY ANTI-SEIZE COMPOUND AROUND THE HEAD IN THIS AREA ONLY CYLINDER HEAD CYLINDER ROD Figure 2-17. Lift Cylinder Internal Component Assembly Cross-Section. SECTION 2 - SERVICE PROCEDURES 2.9 MAST ASSEMBLY AND DISASSEMBLY PROCEDURES The VP Series personnel lift mast sections are contructed of extruded aluminum, protected with an anodized surface finish. The mast sections are interlocked into each other when assembled, by internally mounted slide pads at the top and bottom of each mast section.
These slide pads run up and down in slide pad channels on each side of the mast. SECTION 2 - SERVICE PROCEDURES 5. Carefully slide mast section-3/-4/-5 out BOTTOM of mast section-2/-3/-4 rails. Disassemble slide pads, shims and cable anchor plate from mast section-3/4/-5, if necessary. While mast section-3 is still extended from section-2 remove the bolts attaching the two (2) cable assembly anchor eyelets to the TOP of mast section-3. Remove cables.
NOTE: Steps 6 through 10 apply to removal of mast section4 on model 20VP lifts which have five (5) mast sections. SECTION 2 - SERVICE PROCEDURES Figure 2-19. 10VP Mast Assembly. SECTION 2 - SERVICE PROCEDURES Figure 2-20. 15VP Mast Assembly. SECTION 2 - SERVICE PROCEDURES Figure 2-21.
20VP Mast Assembly. SECTION 2 - SERVICE PROCEDURES Mast Assembly sure there are no air gaps (on flat side of slide pad) between shims, shim and mast or shim and slide pad when tightened. (See Figure 2-18., 2-19., 2-20.
Place mast section-1, rail (open) side up on a clean, flat surface (preferably a table or work bench capable of supporting the weight of the entire mast assembly). Slide mast out over end of work surface far enough to allow access to the chain anchor attach holes at top of mast. SECTION 2 - SERVICE PROCEDURES bracket). Attach using outer set of holes in bottom of mast section-3 with two (2) 1/4'-20UNC x 3/4' long bolts, place a flatwasher under head of each bolt. On outside of spacer tubes place a sheave pin attach bar, (rectangular plate with threaded holes on each side of pin bore hole). Before sliding this assembly into the top of mast section two, locate two (2) mast extension cable assemblies and lay their anchor ends into the slots of the cable mounting tube. SECTION 2 - SERVICE PROCEDURES this manner, due to the tight fit of the slide pads in the slide pad channels, the anodized finish could be removed from the receiving mast’s slide pad channels.
Insert slide pads into the top end mast rails between section-2 and -3, (one on each side of the mast), with beveled surface facing inward towards section3. SECTION 2 - SERVICE PROCEDURES e.
Holding complete cable sheave wheel assembly, slide assembly into top of mast section-4 and align threaded holes in sheave pin attach bars with holes in mast rails. Attach to top of mast section-4 using two (2) 3/ 8'-16UNC x 1/2' long socket head-countersunkflathead cap screws, each side. Coat threads with Loctite #171 and tighten. Locate the remaining mast section-4/-5 (platform mounting- mast section). Lay mast section on flat stable surface. SECTION 2 - SERVICE PROCEDURES g. When mast slide pads are shimmed properly, there should be no side to side movement of slide pad in rail channel.
Mast sections should be very snug in channels but still be able to slide in channel by hand. Slide mast section-4/-5 to top of section-3/-4. Insert threaded ends of cable assembly (attached to top of mast section—2/3) through the chain/cable anchor plate located on bottom of extended mast section-4/-5. SECTION 2 - SERVICE PROCEDURES control valve in the extend (left) port on bottom of hydraulic cylinder. Install a long 90° elbow fitting on return (right) port. Use sealant tape on fitting threads.
Jlg 20mvl Specs Pdf
Cap ports until hydraulic lines are installed. Carefully set machine in an upright position on its base frame wheels. Locate the mast support bracket. Attach mast support bracket to mounting holes halfway up back of mast using four (4) 3/8'-16UNC x 2-3/4' long hex head bolts, locknuts and flatwashers.
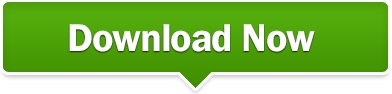